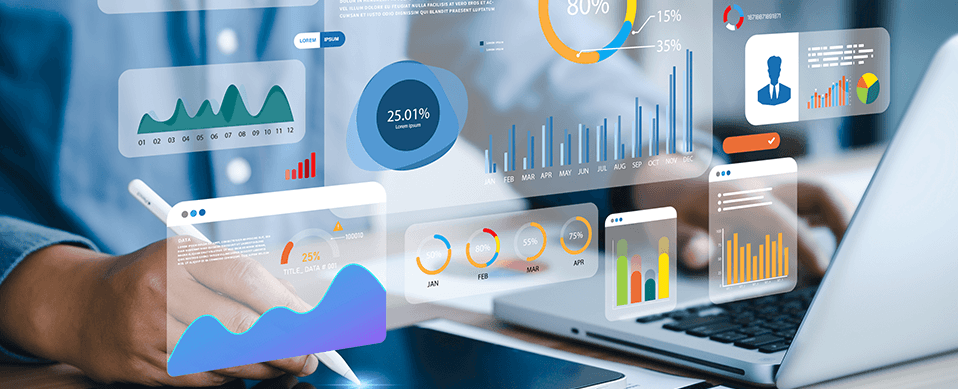
Our
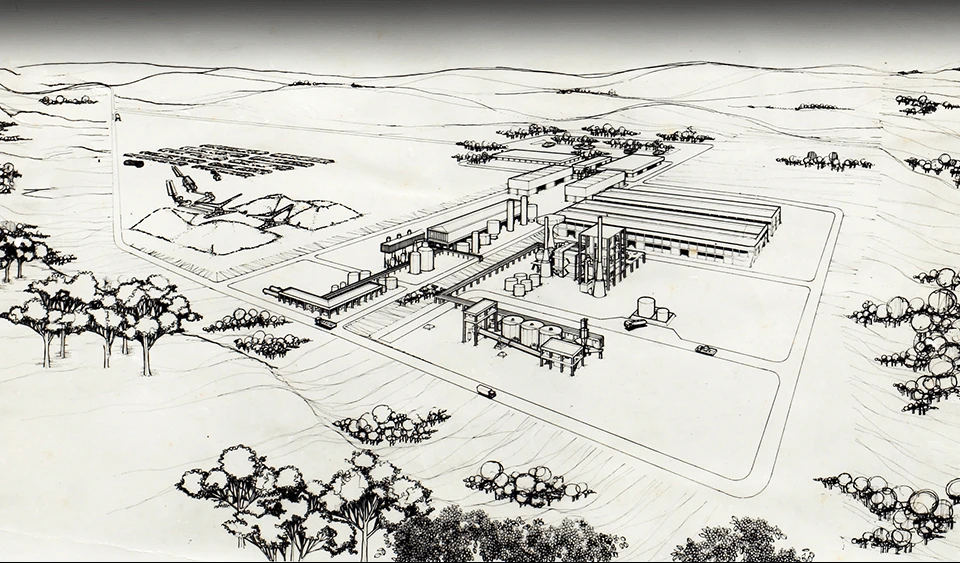
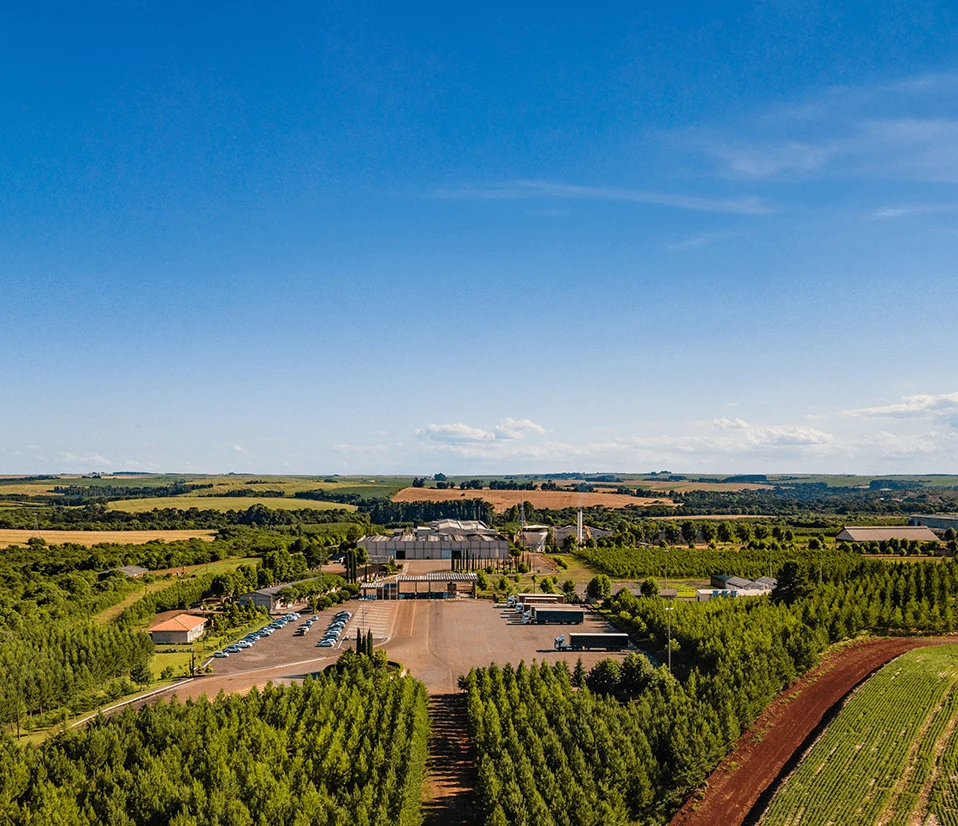
Our
Mission
We work sustainably, developing products and services for a global market of demanding consumers. We make dreams come true with respect and integrity, seeking the constant progress of society.
Vision
To be a group admired for its ability to promote extraordinary results.
Values
Entrepreneurship
Focus on results
Innovation
Integrity
Customer orientation (internal and external)
Financial optimization
Social and environmental responsibility
Safety at work.
Integrated System of
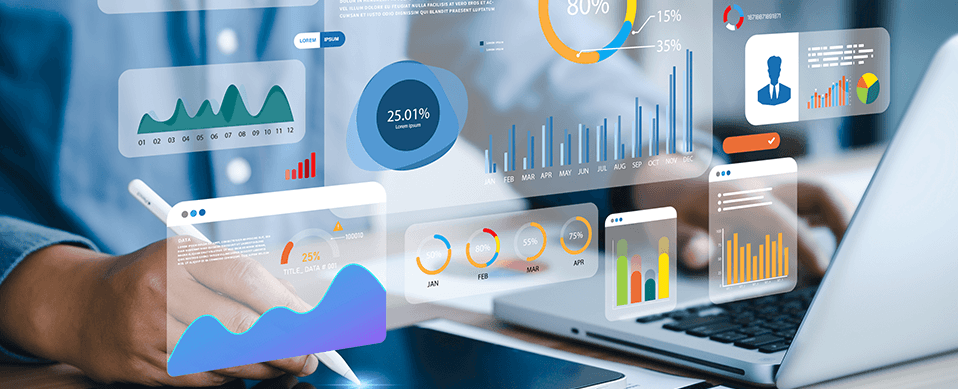
The IMS (Integrated Management System) allows the company to manage all its documents electronically. It is also responsible for managing the 5S audits of its business units. In addition, it assists other areas in the management of certifications such as the FSC ®.
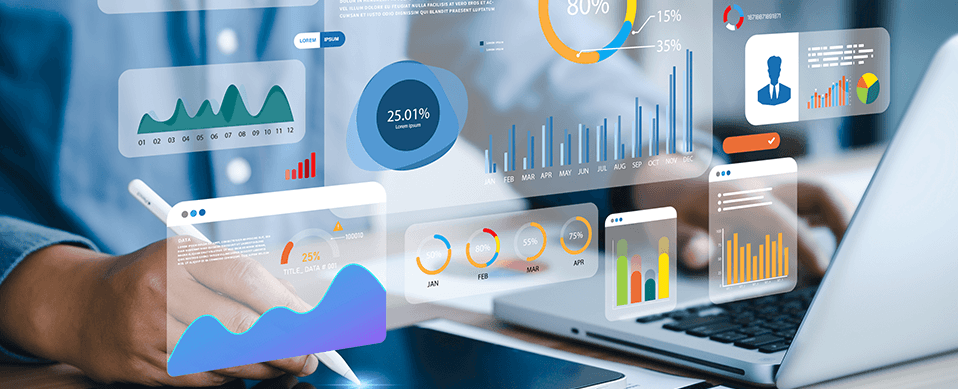

5S is a Japanese culture of good habits aimed at eliminating waste. It operates based on five principles, or pillars:
- Sort (Seiri);
- Set in Order (Seiton);
- Shine (Seiso);
- Standardize (Seiketsu);
- Sustain (Shitsuke).
This methodology aims to improve the work environment by properly disposing of materials, especially unnecessary ones, organizing and cleaning the workplace, identifying spaces, establishing standards for maintaining cleanliness, ensuring discipline, and continuously improving the process.
Santa Maria Group has been working with the 5S methodology since 2004, and all its sectors have it and practice it on a daily basis, enjoying the benefits that the methodology brings.
A computerized business management system that integrates all areas and businesses, making management information reliably available without the need to use parallel programs. This system makes it easier for everyone in the Santa Maria Group to manage information.
Document Management System (DMS) — a tool for managing the Group’s documents.
Santa Maria has the Improvement Suggestions Program, which aims to foster an organizational culture of continuous improvement. It encourages employees to propose enhancements to their processes, workplace, or equipment, with the goal of reducing losses and/or increasing productivity. The company recognizes employees who suggest innovations or changes in their respective areas.
By participating in this program, employees can contribute their ideas to the company’s development and improved performance.
TPM (Total Productive Maintenance) is a methodology that seeks to maximize the efficiency of equipment and production processes by promoting integration between maintenance and operation. Its main objectives include reducing faults, optimizing the use of machines, improving product quality, and increasing productivity through the involvement of all employees. For Santa Maria, TPM is essential as it contributes to cost reduction, greater operational reliability, safety at work, and the creation of a culture of continuous improvement, resulting in greater competition in the market.

5S is a Japanese culture of good habits aimed at eliminating waste. It operates based on five principles, or pillars:
- Sort (Seiri);
- Set in Order (Seiton);
- Shine (Seiso);
- Standardize (Seiketsu);
- Sustain (Shitsuke).
This methodology aims to improve the work environment by properly disposing of materials, especially unnecessary ones, organizing and cleaning the workplace, identifying spaces, establishing standards for maintaining cleanliness, ensuring discipline, and continuously improving the process.
Santa Maria Group has been working with the 5S methodology since 2004, and all its sectors have it and practice it on a daily basis, enjoying the benefits that the methodology brings.
A computerized business management system that integrates all areas and businesses, making management information reliably available without the need to use parallel programs. This system makes it easier for everyone in the Santa Maria Group to manage information.
Document Management System (DMS) — a tool for managing the Group’s documents.
Santa Maria has the Improvement Suggestions Program, which aims to foster an organizational culture of continuous improvement. It encourages employees to propose enhancements to their processes, workplace, or equipment, with the goal of reducing losses and/or increasing productivity. The company recognizes employees who suggest innovations or changes in their respective areas.
By participating in this program, employees can contribute their ideas to the company’s development and improved performance.
TPM (Total Productive Maintenance) is a methodology that seeks to maximize the efficiency of equipment and production processes by promoting integration between maintenance and operation. Its main objectives include reducing faults, optimizing the use of machines, improving product quality, and increasing productivity through the involvement of all employees. For Santa Maria, TPM is essential as it contributes to cost reduction, greater operational reliability, safety at work, and the creation of a culture of continuous improvement, resulting in greater competition in the market.